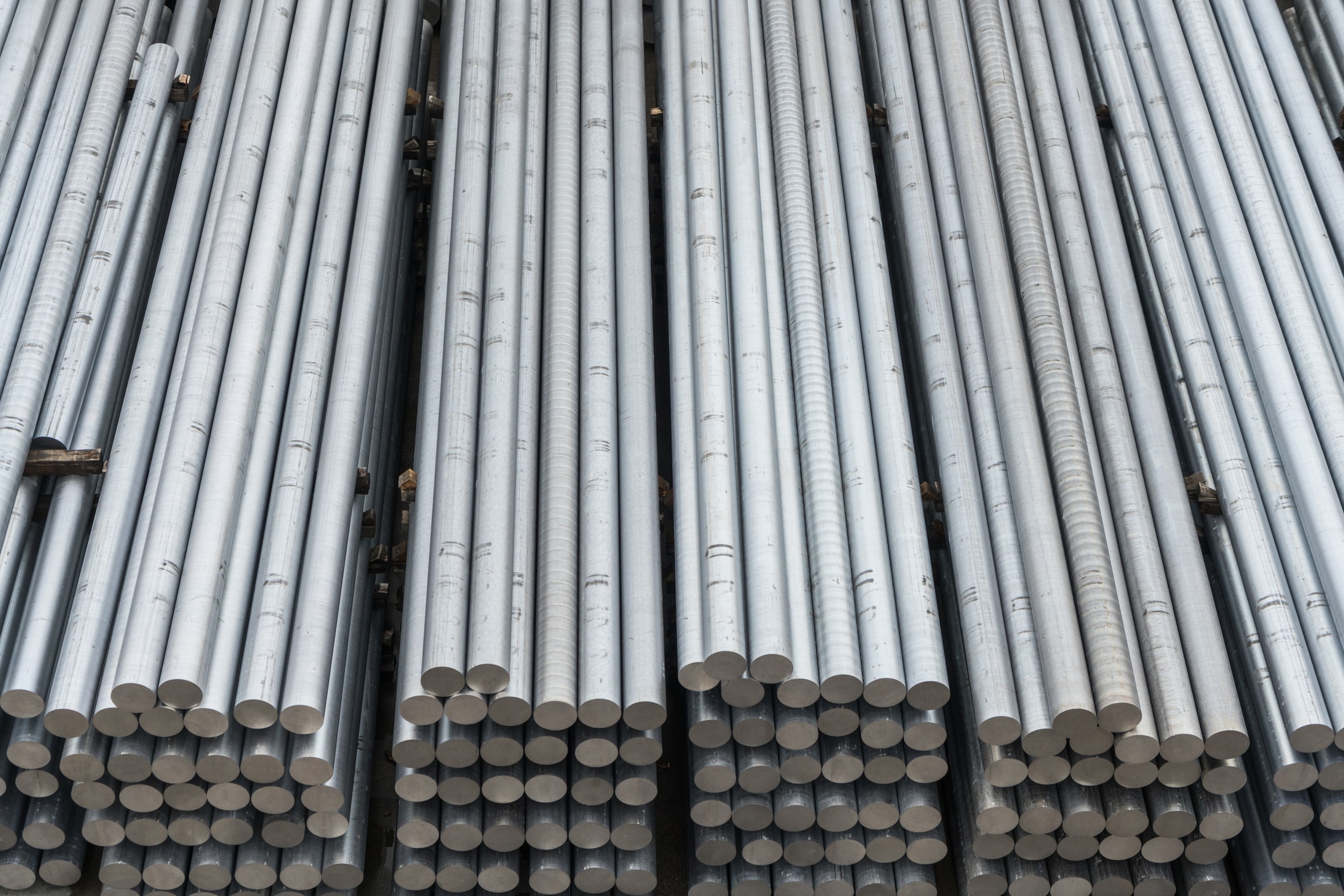
4140 Alloy Round Bar vs. Other Alloy Steels: Key Differences and Benefits
When you need steel for your next project, you must ensure the material is built to handle your specific needs. Steel comes in a variety of shapes, sizes, and alloys, and each one is best suited for various applications.
One of the most versatile and reliable options is 4140 steel. This particular grade is notable for its exceptional hardness, durability, and machinability. At Specialty Steel, you can get this metal in either flat, square, hex, or round bars, depending on your needs.
But is 4140 steel right for your project? Let’s see how it stacks up against other common steel alloys so you can make an informed decision when sourcing your raw materials.
What is 4140 Alloy Round Bar?
First, 4140 is a medium-carbon alloy steel that’s mixed with chromium and molybdenum. The added chromium (typically between 0.8 and 1.1 percent) helps improve the material’s corrosion resistance, hardness, and wear resistance. The added molybdenum (between 0.15 to 0.25 percent) improves the overall strength and toughness of the steel.
But what are the advantages of using 4140 alloy round bars? Round bars are helpful for projects where you need steel in a cylindrical shape. For example, if you’re making pistons or hydraulic gears, you don’t have to shape the material to get it to fit in the machinery. Thanks to the chromium, these bars won’t wear out when deployed in heavy-use scenarios.
Best of all, with Specialty Steel, you can customize the length and diameter of your bars so they require less machining, saving you valuable time.
Comparing 4140 Alloy to Other Alloy Steel
Although 4140 alloy steel is excellent for many unique applications, it may not be the right material for your needs. So, let’s break down the various specifications of this steel compared to other varieties.
4140 Steel vs. 4340 Steel
The chemical makeup of both 4140 and 4340 steel is remarkably similar, to a point. Here’s a quick table so you can see each composition side-by-side.
Element | 4140 Steel % | 4340 Steel % |
Carbon | 0.38 to 0.43 | 0.37 to 0.43 |
Manganese | 0.75 to 1.00 | 0.6 to 0.8 |
Silicon | 0.15 to 0.35 | 0.15 to 0.3 |
Phosphorus | Max 0.035 | Max 0.03 |
Sulfur | Max 0.04 | Max 0.04 |
Chromium | 0.8 to 1.10 | 0.7 to 0.9 |
Molybdenum | 0.15 to 0.25 | 0.2 to 0.3 |
Nickel | N/A | 1.65 to 2 |
As you can see, the most significant difference between the two metals is the addition of nickel to 4340 steel. Also, 4140 has slightly more chromium and slightly less carbon.
Because 4340 has nickel, it’s more resistant to fracturing and wear and tear. So, this metal is perfect for projects where repeated abuse, including environmental hazards, is common. Also, 4340 steel is a bit easier to form and machine, making it slightly more flexible and versatile than 4140.
Overall, 4340 is mainly deployed in the automotive and aerospace industries for crankshafts, rotors, transmissions, and turbines. It can also work well for blade applications.
4140 Steel vs. AISI 4130 Steel
Technically, you can compare 4140 to its other numerical counterparts, 4130 and 4150. In both cases, the chemical composition is the same compared to 4140. However, the number reflects the amount of carbon present in the metal. The lower the number, the less carbon, and vice versa.
Adding carbon to steel makes it harder and tougher, but the trade-off is that it’s less machinable and formable. So, if you want a medium-carbon steel that is more malleable, choose 4130. However, if you need a stronger steel that can handle high-stress situations more easily, choose 4150.
As you might imagine, 4140 is a happy medium that is strong and resilient but relatively easy to shape.
4140 Steel vs. 6150 Steel
If you were to look at another table comparing the chemical compositions of 4140 and 6150 steel, they would look nearly identical for most of the table. However, they differ in a few crucial areas.
First, 6150 steel has more carbon, making it harder. It also doesn’t have molybdenum, which helps make the material more machinable. Instead, it contains vanadium (between 0.15 to 0.3 percent), which makes the metal more heat and wear-resistant.
Typically, 6150 steel is used in shafts, gears, and pistons that experience a lot of stress. While 4140 steel can work in these situations, it doesn’t have the same heat resistance, so it can potentially break or shear when used in heavy-duty applications.
4140 Steel vs. 8620 Steel
Much like 4140 steel, 8620 steel contains chromium and molybdenum to help with its hardness and wear resistance. However, unlike 4140 steel, 8620 contains nickel and has much less carbon (between 0.18 to 0.23 percent).
Where 8620 steel shines is in its case and core toughness. While it’s not as hard or strong as 4140, it can hold its shape very well when used for gears, shafts, and axles. However, this steel is not suitable for high-stress situations as it will bend or break.
What is 4140 Alloy Steel Used For?
Thanks to its robust chemical composition, 4140 alloy steel is something of a “jack of all trades.” This metal can work well in almost any situation or industry, including:
- Agricultural
- Automotive
- Aerospace
- Oil and Gas
- Construction
- Mining and Earth Moving
- Medical Equipment
This alloy is naturally scratch and wear-resistant and sheds microbes easily, making it an ideal choice for medical devices and other equipment. Unless your project requires extra heavy-duty metal, 4140 should work well.
Get Your 4140 Steel From Specialty Steel
At Specialty Steel, we offer quality assurance on all of our orders. Each batch of 4140 steel is fully traceable, so you can feel confident that you’re getting the best materials possible. We also strive to provide the best customer service experience so you always know that we have your back. Contact us to discuss your steel needs today!