As you start sourcing metal for your next project, you know how crucial it is…
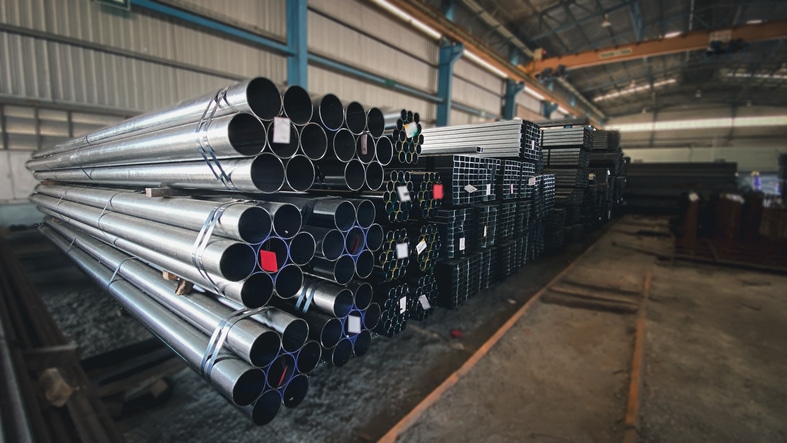
316L Stainless Steel: Best Practices for Welding and Fabrication
When buying steel for your next project, you already know that the type of metal you buy can make a huge difference. However, because you won’t be able to get the material prefabricated and shaped, you’ll need to handle welding and machining on the job site.
316L stainless steel is a valuable and versatile metal, but it requires care and attention to detail to ensure the best welding results. To help you get it right and protect your investment, let’s break down the different best practices when utilizing 316L stainless steel.
A Brief Overview of 316L Stainless Steel
There’s a reason why 316 stainless steel is so widely used across various industries. There are several reasons for this metal’s reliability and versatility, including:
- Corrosion Resistance: Whether deployed in marine environments, food service, or the medical field, 316L stainless steel is designed to withstand corrosion. Best of all, it can handle harsh chemicals and seawater without pitting or rusting.
- Heat Resistance: 316 stainless steel can hold its shape at temperatures up to 1,400 degrees Fahrenheit, making it ideal for high-friction environments, machining, and welding.
- Durability: 316 stainless steel can take a beating and keep on ticking. Its hardness rating is 290 BHN, and its tensile strength is 80,000 psi, so that it can handle almost anything.
Read More: Why Choose 316 Stainless Steel? 316 Stainless Steel Properties and Benefits
Best Practices for Welding 316L Stainless Steel
At Specialty Steel, you can buy 316L stainless steel in rods or sheets and choose custom shapes and sizes to fit your needs. However, when welding different pieces together, selecting the correct methods, materials, and processes is imperative. Here’s a brief overview of the best practices for ensuring a smooth and resilient weld.
Surface Preparation
Dirty, wet, or greasy surfaces can lead to subpar welds. The metal may sometimes not bond correctly, leading to potentially dangerous situations where the weld can come apart.
Ideally, you’ll perform all welds in a controlled environment where dust, dirt, debris, and water vapor are not an issue. While you can weld on the job site, there may be too many variables to consider. If you don’t have a choice, prepare the surface and implement strategies to keep it clean throughout the welding process.
Read More: Surface Treatments for 316 Stainless Steel
Using the Right Welding Materials
Because you’re choosing 316L stainless steel for its hardness, corrosion resistance and reliability, you must ensure the welds are as resilient. Therefore, you must use a stainless steel filler to ensure no weak points throughout the weld.
Different Methods of Welding 316L Stainless Steel
You need to use highly experienced welders when welding 316L stainless steel. Because this material is tricky to weld correctly, you can’t afford errors or setbacks, especially if the steel is deployed in high-intensity environments.
Three primary welding methods work well for this material. Each one has its pros and cons, so here’s a quick overview:
- TIG Welding: TIG welding is by far the most resilient and best-looking option. If you’re using steel pieces in aesthetic areas, you should rely on TIG welders to create immaculate results. The downside, however, is that this welding method is the slowest and most expensive, so it can delay a project and inflate your budget.
- MIG Welding: MIG welding is the second-best option because it’s so reliable, but it doesn’t necessarily look as clean or pristine as TIG welding. Also, finding high-quality welders is faster and easier, so you can finish your project sooner and still get excellent results.
- StickWelding: If you’re working on a tight budget and your welds won’t be experiencing high-stress environments or impacts, stick welding can be a suitable and affordable option. This method is the quickest and easiest, but it doesn’t yield smooth or pristine welds.
Potential Dangers of Welding 316L Stainless Steel
Although stainless steel is relatively easy to weld, it can be tricky in some situations. The two main issues to consider are heat concentration and thermal expansion. Because 316L stainless steel doesn’t conduct heat very easily, the metal can overheat if a welder takes too long in a single space. Overheating can weaken the metal’s structure, potentially ruining the weld.
Thermal expansion occurs because metal expands and contracts based on its temperature. If a welder moves too quickly or too slowly, the sudden changes in heat can cause warping and distortion.
Overall, investing in high-quality welders who are experienced in working with 316L stainless steel can help prevent these issues and ensure better results.
Best Practices for Machining and Fabricating 316L Stainless Steel
While welding allows you to merge multiple pieces, machining will enable you to shape and cut the material to fit your project’s needs. Again, because 316L stainless steel is so complex and has such excellent heat resistance, you must take care when machining it. Here are some points to consider:
- Tool Material: Carbide tips and tools are often preferred for stainless steel machining because they’re more challenging and will retain their shape during the cutting, punching, or drilling process.
- Heating and Cooling: As we mentioned, stainless steel can overheat quickly, so it’s imperative to use a coolant and other methods to keep the metal from bubbling, warping, or melting.
- Tool Speed: Your tool’s RPM can make a huge difference. Too fast, and it may cause too much friction and heat. Too slow, and it can harden the surface, making it more challenging to machine. Choose the right speed based on the tool being used, the steel’s thickness, and the space’s size.
Get Your 316L Stainless Steel From Specialty Steel
Knowing how to machine and weld 316L stainless steel doesn’t matter if you buy subpar materials. At Specialty Steel, we offer full traceability for our metals, so you can feel confident that you’re getting the best option possible. Our customer service team is always available to help you find what you need, including custom shapes and sizes for your steel. Call us for a quote!