Although steel is a reliable material, not all steel is created equally. Depending on what…
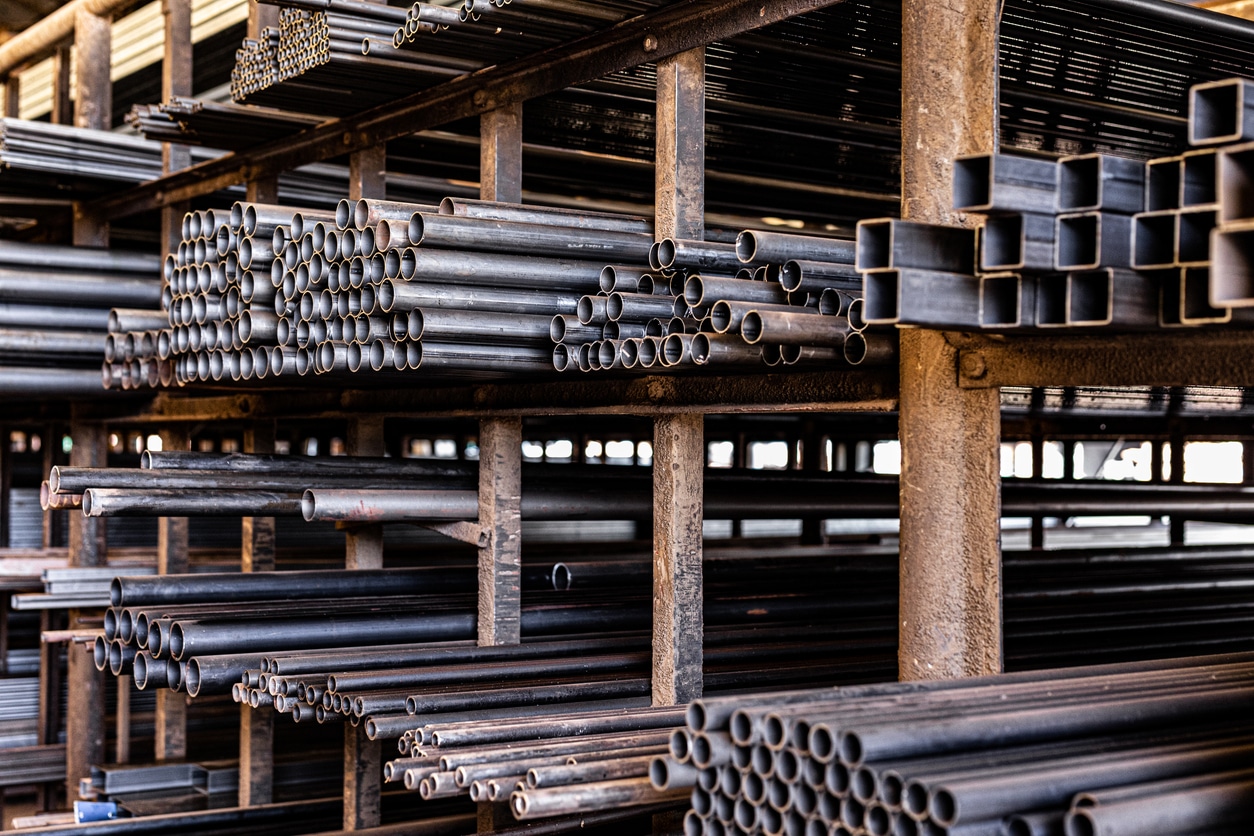
Exploring Carbon Steel Types and Their Role in Modern Manufacturing
When looking for high-quality steel for your next project, you must ensure it’s tough enough to get the job done. However, steel can come in various types, grades, and sizes, meaning you must know the differences to make the right choice.
Carbon steel is a common material used in modern manufacturing, but it comes in several types based on how much carbon it has (among other variables). The more you know about these carbon steel types, the easier it is to pick them. So, let’s break them down and see how they work in modern manufacturing.
An Overview of Carbon Steel Types and Their Uses
Typically, carbon steel can be categorized into three types: low, medium, and high carbon. There is also ultra-high carbon steel, but it’s not as widely used in manufacturing. Here’s an overview of the specific elements of each type.
Low-Carbon
Low-carbon steel has a carbon content between 0.05 and 0.25 percent. Because there’s so little carbon in the material, it’s much softer and more ductile than other types of steel. This category is also very easy to weld.
Because low-carbon steel is so malleable, it’s unsuitable for applications requiring hardness or tensile strength. Instead, it works well for auto body parts, wiring, and structural shapes. The steel’s machinability also makes it ideal for consumer products and appliances, as it’s easy to form small, complex parts.
Medium Carbon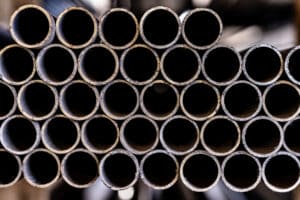
Medium carbon steel has between 0.25 and 0.6 percent carbon, making it noticeably more complicated and durable than low-carbon varieties. The trade-off is that the metal is tougher but not as ductile and is slightly harder to weld.
That said, medium-carbon steel is still not strong enough for many industrial and high-impact applications. Instead, it works well for automotive parts like gears and shafts. This material is also widely deployed for railroad tracks, as it’s easy to machine and can bend according to railway specifications.
High Carbon
High-carbon steel contains between 0.6 and 1.4 percent carbon. This extreme and impact-resistant metal makes it suitable for many industrial and commercial applications. Welding and machining high-carbon steel is challenging, but the results are much stronger and more resilient than lower-carbon alternatives.
High-carbon steel is often used in buildings as reinforcement and support structures thanks to its toughness and hardness. It also works well for cutting blades and high-tension springs in equipment.
Ultra-High Carbon
Ultra-high carbon steel typically has between 1.25 and 2.1 percent carbon. While the extra carbon makes the material particularly hard, it’s also much more brittle. Machining and welding ultra-high carbon steel is difficult, so it’s often not used for manufacturing and industrial purposes. Instead, this type of carbon steel is reserved for specialty parts or knives.
How to Choose the Right Carbon Steel for Your Needs
One of the main challenges of choosing carbon steel is balancing its hardness with its ductility and machinability. As the carbon content increases, the steel gets harder but becomes more brittle and more complex to shape. Medium- and high-carbon steel are the best choices for manufacturing and industrial applications.
Here are some factors to consider when comparing carbon steel types:
Chemical Composition
Carbon is just one component of steel. Materials like manganese, silicon, sulfur, molybdenum, and chromium can be added for various reasons. For example, untreated carbon steel can rust easily, so adding an element like chromium can help improve the metal’s corrosion resistance.
Welding and Machinability
One of the best ways to tell which carbon steel type you need is to determine how much welding and machining you’ll need to do during your project timeline. In some cases, medium-carbon steel might be the better option if you have to weld many pieces together. However, high-carbon varieties might be ideal if you’re not machining the steel too much.
Environmental Considerations
Just because carbon steel can take a beating doesn’t mean it’s well-suited to handle environmental wear and tear. For example, if you’re using this material in a marine environment, you must take extra precautions to ensure it doesn’t rust and corrode.
One of the main questions is whether the metal will be deployed outside or inside. If you’re not using steel with added chemicals to make it wear-resistant, you should add a coating to protect the material and extend its longevity.
Impact Resistance vs. Abrasion Resistance
Although hardness and durability seem like interchangeable terms, they’re technically unique. Hardness refers to how well a material can handle impacts, while durability refers to how well a material can handle rubbing and scraping.
Generally speaking, high-carbon steel is the best at both, making it ideal for applications where the material will experience a lot of wear and tear. If the steel is too soft and malleable, it can deform quickly, causing many issues, particularly if used in complex machinery and equipment.
Sizing and Thickness
Although carbon steel types can tell you a lot about a particular piece of metal, you must also consider the size and thickness of the material. As you might expect, thinner sheets and rods can bend and break more easily than thicker ones. However, thick pieces of carbon steel are more complex to machine and weld, so you must find the right balance when choosing your materials.
Buy Carbon Steel From Specialty Steel
If you’re already starting to feel overwhelmed by all the carbon steel possibilities, don’t worry! At Specialty Steel, we aim to ensure you get the best metal for your needs, regardless of the situation. Our customer support team is always available to answer your questions and help you figure out the right type for each project.
We also offer carbon steel in custom sizes, allowing you to reduce your machining and welding load. Once you’re ready to order, contact us, and we’ll get you started!